Product Tour SPC 1500 - 4000 PT
Large diameter, heavy duty Pipe Cutting Machine
WATCH VIDEO
CNC Pipe Cutting Machine for Vessels and Offshore
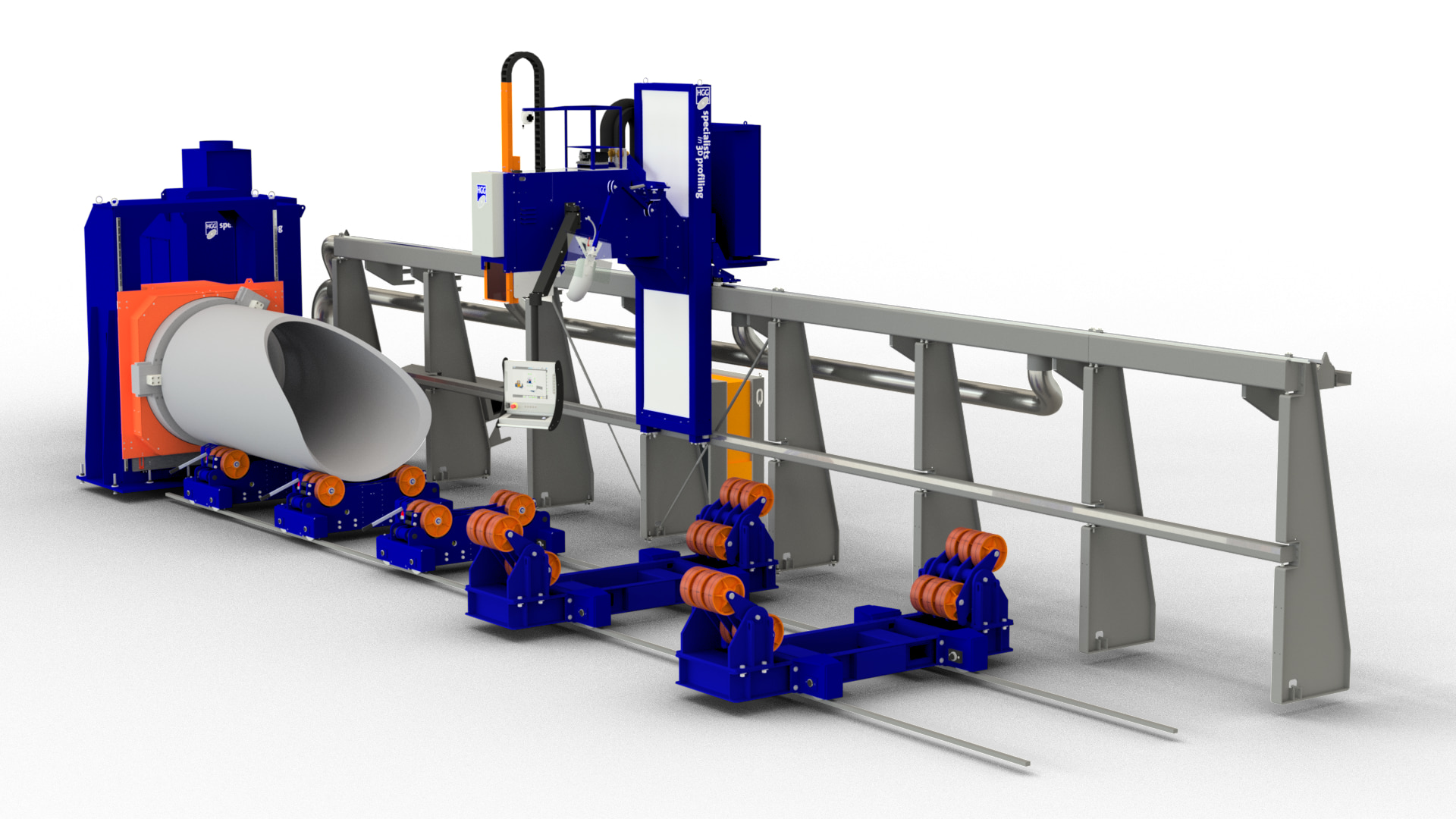
The robust SPC 1500 – 4000 PT Pipe Cutting Machine, driven by a chuck, ensures precise and accurate cutting. It provides the flexibility to handle even the most challenging cuts, such as hillside and elliptical holes, allowing for greater versatility in your layouts and delivering you a higher-quality product at the end of the day.
Specifications
Profile & Dimensions
- Profile
- Machine type
- Minimum
- Maximum
SPC 1500 PT | 100 mm | 1525 mm | |
SPC 2000 PT | 100 mm | 2035 mm | |
SPC 2500 PT | 200 mm | 2500 mm | |
SPC 3000 PT | 300 mm | 3000 mm | |
SPC 4000 PT | 400 mm | 4000 mm |
SPC 1500 PT | 4 “ | 60 “ | |
SPC 2000 PT | 4 “ | 80 “ | |
SPC 2500 PT | 8 “ | 98 “ | |
SPC 3000 PT | 12 “ | 118 “ | |
SPC 4000 PT | 15-1/2 “ | 160 “ |
Additional Specifications
- Oxyfuel Cutting
- High Definition Plasma cutting
- Plasma powersource: Hypertherm or Kjellberg
- Plasma marking with cutting torch
- Maximum Cutting Angle: 70 degrees
- CAD Connection
Discover the possibilities of the SPC 1500 - 4000 PT
Tapered Slot Hole
The SPC-series machines support many different designs of gusset plate connections and weld preparations.
Saddle shapes with advanced beveling for offshore
The SPC-series machines support advanced beveling with a combination of weld types and transition zones.
Crossing Saddle
A saddle shape to connect two crossing pipes, often used in jacket structures.
Production Flexibility
This machine type allows a big range of diameter and wall thicknesses offering you flexibility in production.
Cut with Oxyfuel
Oxyfuel cutting is a reliable, accurate and competitive cutting technique used for the cutting of mild steel. The very first HGG pipe profiling machines, made back in 1984, were equipped with oxyfuel cutting equipment.
Cutting heavy walled pipes with oxyfuel can be a challenging job. And you want to avoid making mistakes during the cutting of these expensive pipes. We developed a gas control system which creates the correct gas mixture based on material and wall thickness. Hot or cold, rusty or clean material, requires different cutting settings. For fine tuning the operator can overrule the gas presets by the dials on the machine interface.
Including pierce assist cutting to get the piercing right each time
The pierce assist function guides the operator to achieve the best combination of torch position, gas mixture and pressure of the pre-heater and the cutting oxygen.
When thick-walled material is pre-heated for too long, the input of oxygen will cause a lot of spatters and create a large crater with an excess of liquid slag. This spatter will stick to the nozzle and negatively affect the gas flow and thus cutting process.
Insufficient pre-heating will mean that the full wall thickness has not reached the ignition temperature to maintain the exothermic process. The process will stop halfway, and the operator will have to try again at another starting point resulting in damage to the part and will cause more time spent on grinding and welding.
or with Plasma
HGG has distinguished itself as a pioneer in CNC plasma cutting. Since 1994, HGG has supplied over 500 3D profiling machines with plasma cutting technology worldwide and keeps innovating with plasma cutting technology to stay on top of the latest developments.
HGG offers unique features that further improve the quality of plasma cutting by compensating for plasma characteristics and/or prolonging consumable lifetime.
We support both Kjellberg and Hypertherm plasma sources. Two well experienced and industry leading choices.
With Angled Piercing technology to protect your plasma consumables
Plasma consumables can become costly if you need to replace them regularly. The angled piercing routine keeps the nozzle and other consumables out of harm’s way, saving you time and money.
Top-of-Class Pipe Cutting Quality Provided by 5 CNC Axes
HGG’s pipe cutting machines achieve precision through five key movements. The combination of all axis ensures top of class cutting quality.
The main drive rotation (1) ensures accurate pipe rotation by securely clamping the pipe to prevent slipping. The longitudinal cutting trolley (2) travels along the entire length of the main frame, enabling precise cuts. The biaxial cutting head (3) rotates to align the cutting torch with the virtual cutting path, and its pitch movements (4) angle the torch to create beveled cuts. Additionally, the cutting head’s height adjustment (5) allows the machine to accommodate pipes of varying diameters while maintaining the correct torch-to-material distance.
Optionally a sixth movement can be added. This transversal movement of the cutting head makes holecutting without pipe rotation, otherwise known as PerfectHole™ technology, possible.
Achieve ultimate precision with our patented biaxial cutting head
The patented biaxial cutting head puts HGG pipe cutting machines in a league of their own. The cutting head, which moves up and down, rotates around its axis, and tilts the cutting torch into the correct position, provides unmatched pipe cutting accuracy. The rotational and pitching movements of the biaxial cutting head, together with the longitudinal movement of the cutting trolley and the height adjustment of the cutting head, provide all the necessary directions for outstanding 3D profiling.
Eliminate Material waste with jaws suited to your needs
The chuck and jaw mounts, designed by HGG, are milled from a solid block of steel, ensuring high material consistency and strength. This contributes to excellent accuracy.
Standard Jaws
The hole through the center of the chuck allows for cutting on both sides of the main drive, depending on the chuck’s maximum hole diameter. The ‘Standard Jaws’ are ideal for this purpose.
Long Jaws
The ‘Long Jaws’ cut on the front side of the main drive, saving scrap length, while ‘Standard Jaws’ require extra pipe length to avoid collisions with the main drive. ‘Long Jaws’ solve this by clamping the pipe further from the main drive.
Zero Scrap Jaws
‘Zero Scrap Jaws’ eliminate the need for extra material. These jaws, protected by copper plates, are perfect for cutting straight chamfers with both X/K bevels and single cuts.
Featured Case Study
The machine helped clean up a lot of our layouts and produce a better quality product at the end of the day.
Kurt Schaerer - Enerflex