Produkt-Tour SPC 1500 - 4000 PT
Large diameter, heavy duty Pipe Cutting Machine
WATCH VIDEO
Patentierter biaxialer Schneidkopf
CNC-gesteuerte Höhenachse
Hochbelastbares Dreibackenfutter
Benutzerfreundliche Oberfläche Maschine
Plasma Schneiden mit Hypertherm oder Kjellberg
CNC Rohr Schneiden Maschine für Schiffe und Offshore
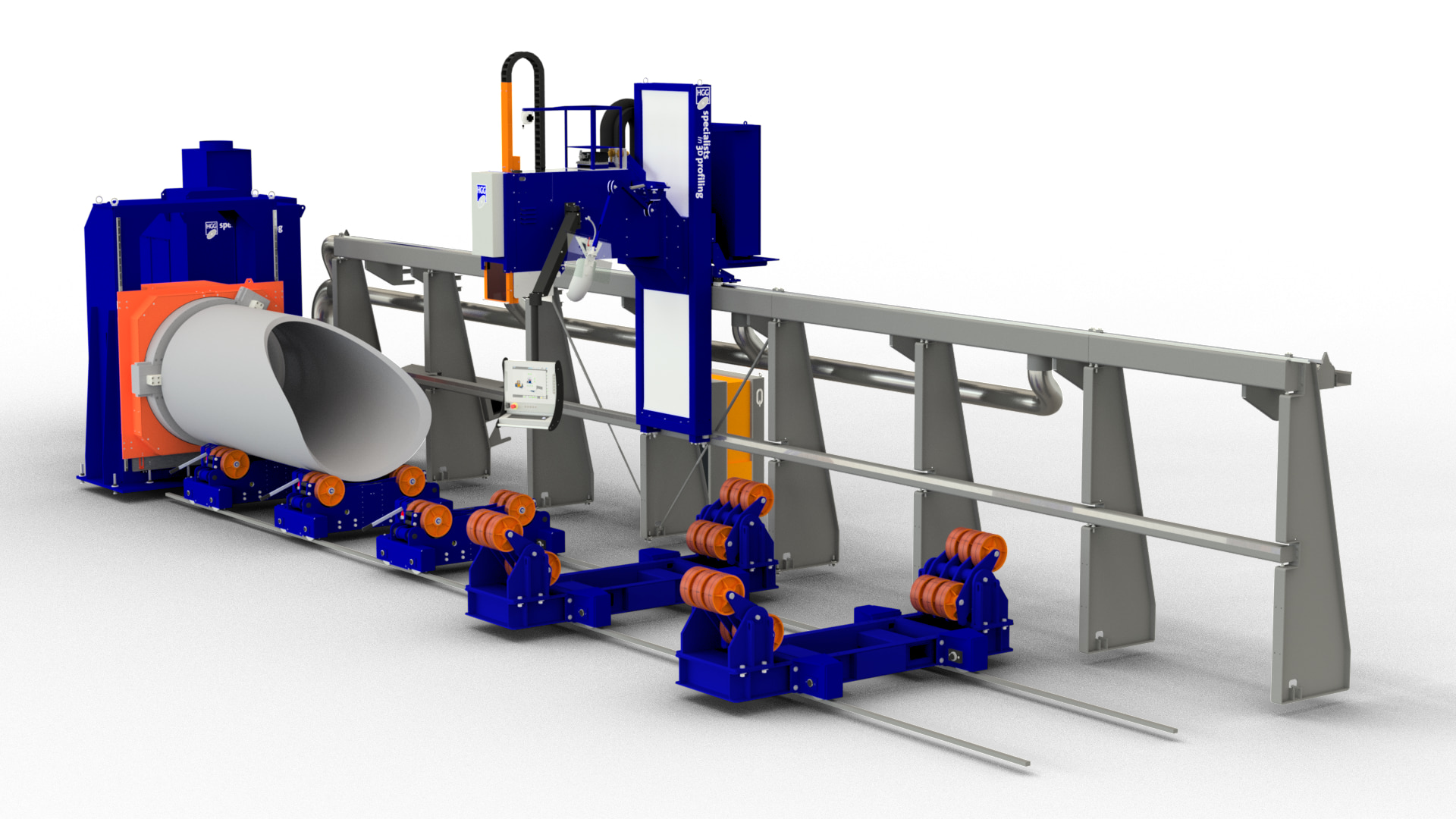
Die robuste SPC 1500 – 4000 PT Rohr Cutting Maschine, die von einem Spannfutter angetrieben wird, sorgt für präzise und genaue Schnitte. Sie bietet die Flexibilität, auch die anspruchsvollsten Schnitte zu bewältigen, wie z. B. bergige und elliptische Löcher, und ermöglicht so eine größere Vielseitigkeit bei Ihren Layouts und liefert Ihnen am Ende des Tages ein qualitativ hochwertigeres Produkt.
Spezifikationen
Profil & Abmessungen
- Profil
- Maschine Typ
- Minimum
- Maximum
SPC 1500 PT | 100 mm | 1525 mm | |
SPC 2000 PT | 100 mm | 2035 mm | |
SPC 2500 PT | 200 mm | 2500 mm | |
SPC 3000 PT | 300 mm | 3000 mm | |
SPC 4000 PT | 400 mm | 4000 mm |
SPC 1500 PT | 4 „ | 60 „ | |
SPC 2000 PT | 4 „ | 80 „ | |
SPC 2500 PT | 8 „ | 98 „ | |
SPC 3000 PT | 12 „ | 118 „ | |
SPC 4000 PT | 15-1/2 „ | 160 „ |
Zusätzliche Spezifikationen
- Oxyfuel Schneiden
- High Definition Plasma schneiden
- Plasma Stromquelle: Hypertherm oder Kjellberg
- Plasma Markierung mit Schneidbrenner
- Maximaler Schneidewinkel: 70 Grad
- CAD-Verbindung
Entdecken Sie die Möglichkeiten des SPC 1500 - 4000 PT
Konisches Schlitzloch
Die Maschinen der SPC-Serie unterstützen viele verschiedene Designs von Knotenblechverbindungen und Schweißnahtvorbereitungen.
Sattelformen mit fortschrittlicher Abschrägung für Offshore
Die Maschinen der SPC-Serie unterstützen fortschrittliches Fasen mit einer Kombination von Schweißtypen und Übergangszonen.
Kreuzungssattel
Eine Sattelform zur Verbindung zweier sich kreuzender Rohre, die häufig in Mantelkonstruktionen verwendet wird.
Flexibilität in der Produktion
Dieser Maschinentyp ermöglicht eine große Auswahl an Durchmessern und Wandstärken und bietet Ihnen Flexibilität in der Produktion.
Schneiden Sie mit Oxyfuel
Oxyfuel Schneiden ist eine zuverlässige, präzise und wettbewerbsfähige Schneidetechnik, die für das Schneiden von Baustahl verwendet wird. Die allerersten HGG-Maschinen zum Profilieren von Rohren aus dem Jahr 1984 waren mit einer Oxyfuel-Schneidanlage ausgestattet.
Das Schneiden dickwandiger Rohre mit Oxyfuel kann eine Herausforderung sein. Und Sie wollen beim Schneiden dieser teuren Rohre keine Fehler machen. Wir haben ein Gassteuerungssystem entwickelt, das je nach Material und Wandstärke das richtige Gasgemisch erzeugt. Heißes oder kaltes, rostiges oder sauberes Material erfordert unterschiedliche Schneideinstellungen. Für die Feinabstimmung kann der Bediener die Gasvoreinstellungen über die Drehregler an der Schnittstelle der Maschine außer Kraft setzen.
Inklusive Einstechhilfe, damit das Piercing jedes Mal richtig sitzt
Die Lochstechhilfe führt den Bediener zur besten Kombination aus Brennerposition, Gasgemisch und Druck des Vorwärmers und des Schneidsauerstoffs.
Wenn dickwandiges Material zu lange vorgewärmt wird, verursacht der Sauerstoffeintrag viele Spritzer und erzeugt einen großen Krater mit einem Überschuss an flüssiger Schlacke. Diese Spritzer bleiben an der Düse haften und beeinträchtigen den Gasfluss und damit den Schneidprozess negativ.
Eine unzureichende Vorwärmung bedeutet, dass die gesamte Wandstärke nicht die Zündtemperatur erreicht hat, um den exothermen Prozess aufrechtzuerhalten. Der Prozess wird auf halber Strecke abgebrochen und der Bediener muss es an einem anderen Ausgangspunkt erneut versuchen. Dies führt zu einer Beschädigung des Teils und verursacht einen höheren Zeitaufwand beim Schleifen und Schweißen.
oder mit Plasma
HGG hat sich als Pionier im CNC-Plasmaschneiden hervorgetan. Seit 1994 hat HGG weltweit mehr als 500 3D-Profiliermaschinen mit Plasmaschneidtechnologie geliefert und hält sich mit Innovationen in der Plasmaschneidtechnologie auf dem neuesten Stand der Entwicklung.
HGG bietet einzigartige Funktionen, die die Qualität des Plasmaschneidens weiter verbessern, indem sie die Eigenschaften des Plasmas kompensieren und/oder die Lebensdauer der Verschleißteile verlängern.
Wir unterstützen sowohl Kjellberg- als auch Hypertherm-Plasmaquellen. Zwei sehr erfahrene und branchenführende Anbieter.
Mit Angled Piercing Technologie zum Schutz Ihres Plasmaverbrauchsmaterials
Plasma Verbrauchsmaterialien können kostspielig werden, wenn Sie sie regelmäßig ersetzen müssen. Durch das angewinkelte Einstechen werden die Düse und andere Verbrauchsmaterialien nicht beschädigt, wodurch Sie Zeit und Geld sparen.
Erstklassige Rohr Schnittqualität durch 5 CNC-Achsen
Die Rohrschneidemaschinen von HGG erreichen Präzision durch fünf Schlüsselbewegungen. Die Kombination aller Achsen gewährleistet eine erstklassige Schnittqualität.
Die Rotation des Hauptantriebs (1) sorgt für eine präzise Drehung des Rohrs, indem sie das Rohr sicher einklemmt, um ein Verrutschen zu verhindern. Der Längsschneidewagen (2) bewegt sich entlang der gesamten Länge des Hauptrahmens und ermöglicht präzise Schnitte. Der biaxiale Schneidkopf (3) dreht sich, um den Schneidbrenner an der virtuellen Schneidbahn auszurichten, und seine Neigungsbewegungen (4) winkeln den Brenner an, um schräge Schnitte zu erzeugen. Dank der Höhenverstellung des Schneidkopfs (5) kann die Maschine außerdem Rohre mit unterschiedlichen Durchmessern bearbeiten und dabei den richtigen Abstand zwischen Brenner und Material beibehalten.
Optional kann eine sechste Bewegung hinzugefügt werden. Diese transversale Bewegung des Schneidkopfes ermöglicht das Schneiden von Löchern ohne Rohrdrehung, auch bekannt als PerfectHole™-Technologie.
Erzielen Sie höchste Präzision mit unserem patentierten biaxialen Schneidkopf
Mit dem patentierten biaxialen Schneidkopf spielen die Rohrschneidmaschinen von HGG in einer ganz eigenen Liga. Der Schneidkopf, der sich auf und ab bewegt, sich um seine Achse dreht und den Schneidbrenner in die richtige Position kippt, sorgt für eine unübertroffene Genauigkeit beim Schneiden von Rohren. Die Rotations- und Neigungsbewegungen des biaxialen Schneidkopfs bieten zusammen mit der Längsbewegung des Schneidwagens und der Höhenverstellung des Schneidkopfs alle notwendigen Richtungen für eine hervorragende 3D-Profilierung.
Eliminieren Sie Materialabfälle mit auf Ihre Bedürfnisse abgestimmten Backen
Das Futter und die Backenhalterungen, die von HGG entwickelt wurden, sind aus einem massiven Stahlblock gefräst und gewährleisten eine hohe Materialkonsistenz und Festigkeit. Dies trägt zu einer hervorragenden Genauigkeit bei.
Standard Backen
Das Loch in der Mitte des Futters ermöglicht das Schneiden auf beiden Seiten des Hauptantriebs, je nach maximalem Lochdurchmesser des Futters. Die ‚Standard Jaws‘ sind für diesen Zweck ideal.
Lange Kiefer
Die ‚Long Jaws‘ schneiden an der Vorderseite des Hauptantriebs und sparen so Schrottlänge, während die ‚Standard Jaws‘ zusätzliche Rohrlänge benötigen, um Kollisionen mit dem Hauptantrieb zu vermeiden. Die ‚Long Jaws‘ lösen dieses Problem, indem sie das Rohr weiter vom Hauptantrieb entfernt einspannen.
Null Schrott Kiefer
Mit den ‚Zero Scrap Jaws‘ brauchen Sie kein zusätzliches Material mehr. Diese durch Kupferplatten geschützten Backen sind perfekt zum Schneiden von geraden Fasen mit X/K-Fasen und Einzelschnitten geeignet.
Ausgewählte Fallstudie
The machine helped clean up a lot of our layouts and produce a better quality product at the end of the day.
Kurt Schaerer - Enerflex