Product Tour RPC 1200 Mk3
The Next Generation Beam Coping Machine.
WATCH VIDEO
Beam Cutting Machine That Cuts It All
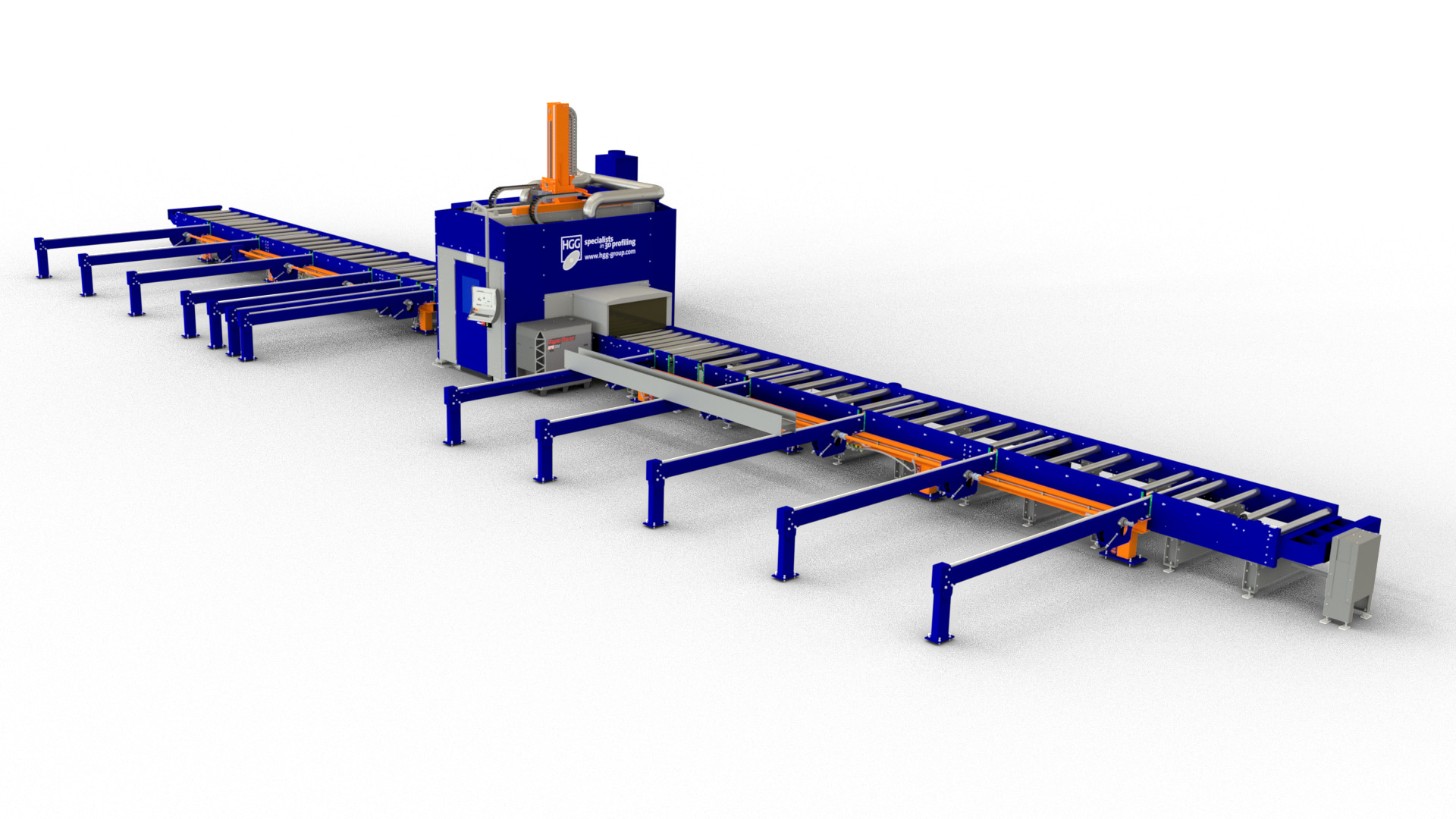
The RPC 1200 Mk3 Robotic Plasma Cutter was originally developed for the offshore market but is equally well-suited to the structural steel industry, meeting the high-speed production demands of fabricators. With HGG’s ProCAM software, you can quickly import NC or STEP data and take advantage of the RPC’s versatility and ability to handle all profile types, including pipes and plates.
Specifications
Profile & Dimensions
- Profile
- Minimum
- Maximum
100 x 5 mm | 457 x 25 mm | |
100 x 100 mm | 600 x 400 mm | |
100 x 50 mm | 1220 x 430 mm | |
100 x 50 mm | 475 x 150 mm | |
100 x 50 mm | 140 x 140 mm | |
75 mm | 300 mm | |
100 x 50 mm | 200 x 100 mm | |
100 x 6 mm | 430 x 20 mm | |
100 x 15 mm | 400 x 40 mm |
4 x 1/4 “ | 18 x 1 “ | |
4 x 4 “ | 24 x 16 “ | |
4 x 2 “ | 48 x 17 “ | |
4 x 2 “ | 18-6/8 x 5-7/8 “ | |
4 x 2 “ | 5-1/2 x 5-1/2 “ | |
3 “ | 12 “ | |
3-7/8 x 2 “ | 16 x 1-5/8 “ | |
4 x 1/4 “ | 17 x 3/4 “ | |
3-7/8 x 5/8 “ | 16 x 1-5/8 “ |
Additional Specifications
- Hi-Def plasma by default
- Plasma marking with cutting torch
- Powersource: Hypertherm or Kjellberg
- CHS / Pipe cutting requires additional equipment and is only compatible with HGG Standard conveyers
Discover the possibilities of the RPC 1200 Mk3
Heavy Walled Beams
Make light work of heavy wall thickness with the RPC 1200 Mk3. Even weld preparations can be cut without compromising on our quality standards.
Bolt holes and copes for bolted connections
The RPC applies specialized cutting routines for hole cutting on all profiles, ensuring they meet quality standards like EN1019 and ISO9013, up to EXC3.
Weld Preparations for Welded Connections
Cut complex weld preparations, including K-bevels. We developed special cutting routines for ratholes reducing rework after cutting to a minimum.
Supports most beams, bars and hollow sections
Cut Channels, flat-bar, angle-bar and even hollow sections. Benefit of HGG’s 40 years of 3D profiling expertise.
Precise Robot Positioning by Height and Transversal Axis for Optimal Performance
A transversal axis and a height axis are responsible for the gross industrial robot positioning needed for cutting and marking 360 degrees around the material. The industrial robot will perform the fine movements necessary for accurate torch positioning and bevelling. The combination of the gross robot positioning and the use of a short industrial robot arm for fine positioning results in accurate cuts and rapid torch positioning.
The most precise cut in the market with laser length measurement
To prevent length deviations of cut parts the RPC is equipped with an smart longitudinal laser measurement system. This laser system fits perfectly into the character of this machine, namely fast and accurate.
The end-point of the material is measured by a laser measurement system that defines its longitudinal position. With the initialization point as reference the exact length of the profile is calculated.
Logistics of a typical configuration
The infeed and outfeed conveyors for the cutting cell can be loaded directly by crane or by optional storage chains onto which material can be loaded and unloaded by a crane or forklift.
The infeed conveyor transports profiles until detected by a light sensor after which the infeed conveyor stops. The spacing of the rollers is optimized to cut both long and short parts. Finished parts are transported from the cutting cell to the outfeed conveyor. The outfeed storage chains can store and buffer multiple parts which can be transported to other logistic systems or unloaded by a crane or forklift.
Stitch Cutting on the RPC 1200 Mk3
Sometimes it’s difficult to handle and store parts of different sizes and lengths efficiently. Keeping parts stitched together with a custom cutting routine can lower the crane or fork lifting need because profiles keep their original length. Handling will not interfere with the machine throughput nor become a bottleneck. Another benefit is easy processing of extremely short parts. Some rework (cutting the stitches through) is necessary to separate the parts.
3D Laser Measurement for Material displacement and distortion compensation
The theoretical and actual position and shape of the raw material differ. To achieve an accurate cut and prevent collisions during cutting, the material must be measured.
We have developed an accurate and rapid 3D measuring system that contributes to creating a highly productive and precise cutting machine by identifying distortions in position, torsion, and flange or web angles.
3D Profiling Shapes
H-Beam Cutting
This unique sequence cuts the flange in one motion, avoiding web damage and leaving a smooth, uninterrupted welding surface.
- Plasma Cutting
- Plasma Marking
- Import and view DSTV / NC1 files from any CAD-system
- Material up to 1220 x 430 mm or 48 x 17 “
Channel Profile Cutting
The option to cut channel profiles provides extra flexibility, making the RPC a true all-in-one solution.
- Plasma Cutting
- Plasma Marking
- Import and view DSTV / NC1 files from any CAD-system
- Material up to 475 x 150 mm or 18-6/8 x 5-7/8 “
Box Profile Cutting
The RPC compares theoretical and actual box sizes, cutting the profile in one sequence to boost throughput while maintaining accuracy.
- Plasma Cutting
- Plasma Marking
- Import and view DSTV / NC1 files from any CAD-system
- Material up to 600 x 400 mm or 24 x 16 “
Case Study
Featured Case Study
' “The RPC gave us the opportunity to control our supplies, lead time, and cutting quality.'
Steve Wilkins, Director / jack-of-all-trades, at Solution Steel