Plasma Cutting Compensation for Beams, Bars and Bulbs
Do you want to improve your plasma cutting accuracy? With only a few adjustments, you can improve plasma cutting quality significantly. There are a few ways to improve plasma cutting accuracy. In the article below we describe four steps that might help you to improve your plasma cutting accuracy for beams, bars and bulbs.
Kerf Width Compensation
The width or kerf depends on the plasma cutting system. This kerf is compensated by the software to ensure an even better accuracy. This compensation is typically half of the kerf width.
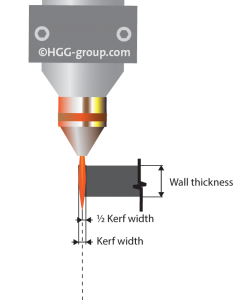
Arc Shape Compensation
In most cutting conditions the plasma arc cuts a convergent kerf; this convergence can vary depending on the plasma torch, nozzle and set torch height. To make sure the cut bevel angle is accurate the convergence can be compensated by a parameter in a machines software. If the convergence of the kerf is 3 degrees with a required bevel of 30 degrees, the cutting angle needs a correction of 1.5 degrees for example. Consequently, the torch angle will be 28.5 degrees compensating for the convergence.
Optimized Cutting Direction
Plasma cutting uses a swirl to focus, stabilize and protect the arc. The swirl creates a ‘good’ and a ‘bad’ side in the kerf. In order to get a straight cut the torch must travel in the proper direction to have the ‘good’ side on the part and the bad side on the remnant material. The good side is on the right relative to the torch’s movement direction. HGG uses this knowledge and adapts the cutting routines to maintain the most accurate cut.
Melting Correction
Especially when cutting a negative bevel the melting away and rounding of the corners occurs on the fit line. Within the software this melting away can be compensated with a numeric variable (mm). This parameter corrects the (local) fit line easing the fitting and welding of the final product.
Interested in automating your cutting with a plasma cutting machine? Have a look at all available CNC cutting machines from HGG.