Automating your pipe profiling process is often beneficial when 3D shapes are required. The automated process is not only time-saving, but also more accurate compared to manual cutting. Complex 3D profiling, like holes, end cuts or lobster backs, with or without weld-preparation, are easily performed with a pipe profiling machine. Smooth and continuous movements, easily achievable with machines, result in cleaner cuts.
For 3D profiling your pipes, HGG machinery utilizes 5 points of movement to create the perfect cut every time!
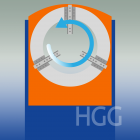
1. Main Drive Rotation
To cut the complete surface of a pipe you have to rotate it around its centerline. Pipe rotation can be performed by rotating it with a driven support or by clamping it with a CNC controlled chuck and rotating it. This provides maximum accuracy and prevents the pipe from slipping.
2. Cutting Trolley Longitudinal
Pipe cutting involves end cuts and intermediate cuts. To cut along the complete longitude of the pipe, you either move the pipe or move your torch. HGG pipe cutting machines move the cutting trolley to the correct position with CNC controlled movement.
3. Cutting Head Rotation
The rotational movement of the biaxial cutting head aligns the torch with the correct plane before tilting the cutting head. Rotating the cutting head is necessary to position the torch for accurate bevels with end and intermediate cuts.
4. Cutting Head Tilt
The tilting movement of the biaxial cutting head positions the torch at the correct angle to perform bevelled end and intermediate cuts. When the cutting torch tilts, the cutting trolley moves longitudinally to compensate for the new torch angle.
The combination of these four movements allows for high precision beveled cutting.
5. Cutting Trolley Height
HGG machines cut a range of different diameters. A combination of the height movement of the trolley and of the chuck allow the full range to be cut. Sensor arms on the cutting trolley maintain a constant torch-to-material distance during cutting, even when cutting distorted pipes. For pipes that are out of shape, mechanical sensor arms prevent the torch from hitting the material.
Cutting Trolley Transversal
In some situations (e.g., vessel head cutting, box section cutting, specific hole cutting), a transversal movement, across the diameter of the pipe, is necessary. This added direction provides the benefit of more reachability, but is generally not necessary.
Distorted pipes, with large seam welds, a bow shape or an uneven ovality across their length benefit from less movement. Especially intermediate cuts can be negatively influenced. By adding transversal movement, intermediate cuts can be performed with minimized rotation of the pipe. HGG calls this PerfectHoleTM technology, and is advised to those who want to maximize their quality output.